Plate bending machines
Hydraulic Four Roller Plate Roll bender
Two Roller Steel Bending Machine
Three Roller Bending Machine
Four Roller Rolling Machine
Profile bending machine
Auxiliary products
Upper Roll Bending Machines
Industry News
Key points for safe and standardized operation of plate rolling machine
A plate rolling machine is a general-purpose equipment that rolls metal plates into cylindrical, arc-shaped or other shaped workpieces. According to the principle of three points forming a circle, the relative position change and rotational movement of the workpiece are used to make the plate produce continuous plastic deformation to obtain a workpiece of a predetermined shape. Almost all steel materials that are formed into cylindrical shapes are rolled by plate rolling machines.
The movement of plate rolling machines can be divided into two forms of movement: main movement and auxiliary movement. The main movement refers to the rotation, bending and other movements of the upper and lower rollers that constitute the plate rolling machine on the processed plate. The main movement completes the processing task of the plate rolling machine. The auxiliary movement is the movement of loading, unloading, lifting, tilting and flipping of the upper roller during the rolling process.
An important point in operating a plate rolling machine is standardization and safety issues. During the use of the plate rolling machine, it is necessary to follow the operating procedures of the plate rolling machine to try to reduce and eliminate the occurrence of dangerous accidents. Let's take a look at how to prevent the occurrence of dangerous accidents.
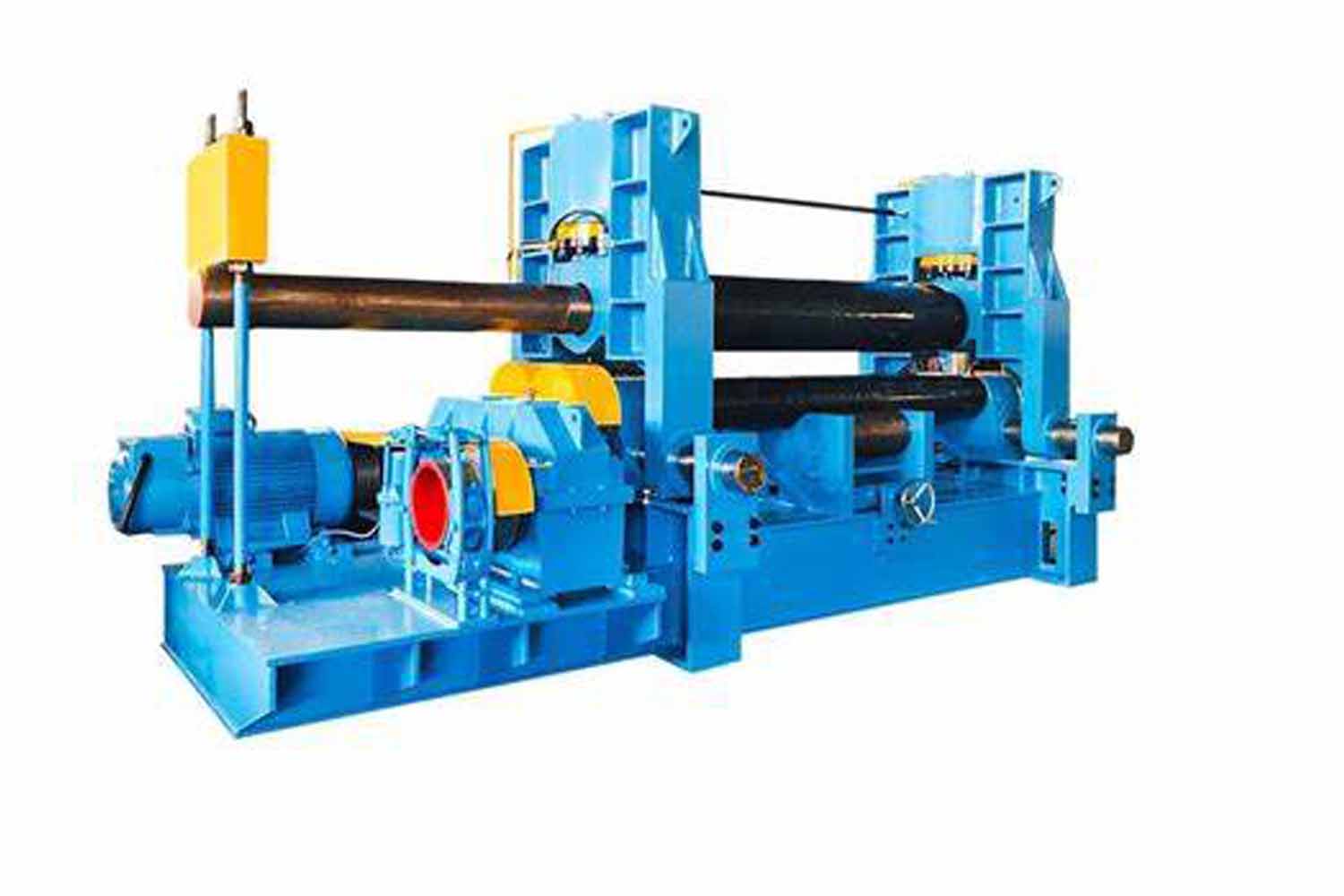
When controlling the distance between the rollers, be sure to pay attention to the rotation of the rollers. Be sure to stop the machine before reaching the limit to avoid accidents.
During the use of the plate rolling machine, the transmission mechanisms and connection parts should be checked and maintained frequently to ensure that they are not loose or damaged. During the bending process, there should be no slippage between the steel plate and the roller surface to prevent the roller surface from being pulled and injured.
During the rotation of the plate rolling machine, if abnormal sounds, vibrations, oil leakage, or impacts are found, the machine should be stopped immediately for inspection. When checking and repairing the hydraulic system, high-pressure oil should be prevented from escaping and hurting others. It is strictly forbidden to make steel plates directly on the machine without flattening the welds and leveling.
When the plate rolling machine is rotating and two or more operators are working at the same time, there must be a dedicated person to direct, and the division of labor must be clear when directing.
When leveling or rolling, the steel plate should be placed in the middle of the working roller, and the thickness of the steel plate should be reduced accordingly when placed aside. No one is allowed to approach when the roller is rotating, and clothes and hands are prohibited from being wrapped in the roller.